Plain Plug Gauges
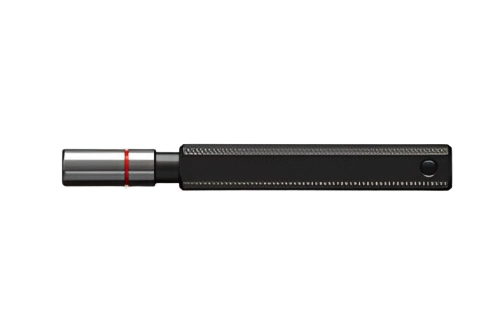
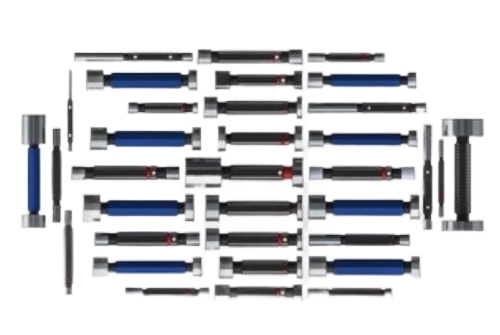
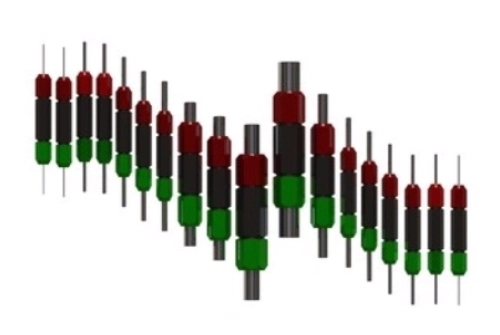
A plain plug gauge is a type of precision measuring tool used to check the internal diameter or hole size of a workpiece. It is commonly used in manufacturing and quality control to ensure that holes or bores in parts are made to specific dimensions and tolerances. Plain plug gauges come in two primary types: go and *no-go* gauges. The “go” gauge checks whether a hole is large enough, while the “no-go” gauge ensures that the hole is not too large.
Uses of Plain Plug Gauges:
Plain plug gauges are used to measure the internal diameters or hole sizes of a workpiece, typically for cylindrical holes, bores, or other internal features. This helps confirm that the part meets the required specifications for fit and function.
These gauges are designed to check if a hole is within the specified tolerance range. They ensure that the hole is neither too tight nor too loose, which could affect the performance of the part in its assembly.
Plain plug gauges are often used in quality control and inspection processes to verify whether the internal diameter of a hole falls within the specified limits (such as for a shaft or bearing fit).
After a part has been machined, the plain plug gauge is used during the final inspection to verify that the part’s internal dimensions meet the design specifications before it is sent for assembly or delivery.
Plain plug gauges are often used to check the fit of inserts, pins, or bushings inside a hole. Ensuring the correct size and fit is crucial for proper assembly and functionality.
These gauges can also be used to calibrate machines (such as boring machines or CNC machines) by ensuring that the machine is producing parts with accurate and consistent hole dimensions.
Plain plug gauges can be used to inspect parts that are subjected to wear and tear, like engine components, to check whether the internal holes still meet the required size after use.
In specific cases, plug gauges can be used to measure *hole depth* in addition to hole diameter, depending on the design of the plug gauge.
Types of Plain Plug Gauges:
This gauge is used to check if the hole is large enough to accept the gauge. It should fit easily into the hole if the hole is within the specified tolerance.
This gauge is used to check if the hole is too large. The **no-go gauge should not fit* into the hole if it is within tolerance. If it does, it indicates that the hole is out of specification.
Advantages of Plain Plug Gauges:
Plain plug gauges are manufactured to tight tolerances, making them highly accurate and reliable for measuring internal diameters or hole sizes. They are essential in industries where high precision is required, such as aerospace, automotive, and engineering.
Plain plug gauges are simple to use, requiring minimal setup or adjustment. The operator can quickly insert the gauge into the hole to verify its size, making the measurement process fast and efficient.
Plain plug gauges are typically made from high-quality, hardened steel or other durable materials, ensuring that they maintain their accuracy over extended periods and with frequent use. Their robust construction makes them resistant to wear and damage.
Compared to other precision measurement tools, plain plug gauges are relatively affordable. Their simplicity, durability, and long service life make them a cost-effective solution for checking hole sizes in high-volume production.
These gauges provide consistent and repeatable results, making them ideal for mass production environments where hundreds or thousands of parts need to be checked. This reduces human error and improves the overall quality of the production process.
Once the plain plug gauge is manufactured to the required specifications, it does not need frequent calibration. As long as the gauge is well-maintained, it will continue to provide reliable measurements without the need for periodic recalibration.
Plain plug gauges allow for fast quality control checks. They can be used to inspect parts rapidly and efficiently, which is particularly beneficial in high-speed manufacturing environments where time is critical.
The plain plug gauge is a non-destructive tool. It simply checks the size of the hole without altering or damaging the workpiece, ensuring that the part remains usable even after inspection.
In high-volume production runs, plain plug gauges are particularly beneficial. Their simplicity and speed make them ideal for quick checks of hole sizes during continuous production, ensuring parts meet dimensional specifications.
Plain plug gauges can be custom-made to check specific hole sizes or tolerances, making them highly versatile and adaptable to a wide range of applications. Whether it is for a specific type of part or a custom-designed hole, plain plug gauges can be tailored to suit the requirements.
Due to their small size and design, plain plug gauges are easy to carry and can be used in various environments, including on-site inspections, field tests, or workshops.
Conclusion:
Plain plug gauges are essential tools in the quality control and manufacturing industries. They provide precise, reliable, and cost-effective solutions for measuring internal hole sizes and verifying dimensional tolerances. The advantages of using plain plug gauges, such as their accuracy, ease of use, and durability, make them indispensable for ensuring the quality of parts in high-volume production environments. Whether for routine inspections or specialized applications, plain plug gauges help maintain consistency and ensure that parts meet the required specifications.